
Delfoi tuottaa suunnitteluratkaisuja ja -palveluja, joilla organisaatiot parantavat kilpailukykyään ja kannattavuuttaan tehostamalla tuotantoprosesseja ja lisäämällä niiden laatua ja läpinäkyvyyttä.
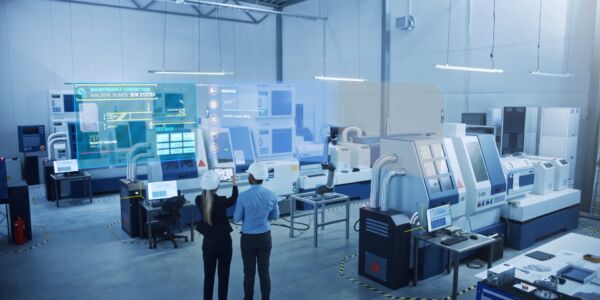

Tuotannon tehostaminen
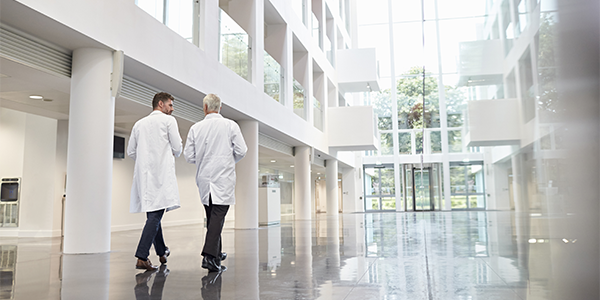

Toiminnan kehittäminen ja suunnittelu
Delfoi Healthcare tarjoaa toiminnan kehittämispalveluita ja
-suunnitteluratkaisuja sosiaali- ja terveydenhuoltoon.
Delfoi Planner on web-pohjainen, helppokäyttöinen ja visuaalinen tuotannonsuunnitteluratkaisu. Se auttaa lyhentämään tuotannon läpimenoaikoja sekä parantamaan tuottavuutta ja toimitusvarmuutta. Ratkaisun avulla parannat toiminnan läpinäkyvyyttä ja reaaliaikaisuutta, sekä helpotat muutoshallintaa.
Delfoi Consulting tarjoaa luotettavan ja nopean tavan kehittää tuotantoa. Simuloinnin avulla mallinnetaan kehitystoimenpiteiden vaikuttavuus etukäteen.
Delfoi Healthcare Consultingin missiona on sujuvoittaa sosiaali- ja terveydenhuollon prosesseja ja asiakasvirtoja. Autamme kehittämään toimintaa asiakaslähtöisemmäksi huomioiden muuttuvat yhteiskunnan tarpeet sekä asiakkaiden odotukset ja vaatimukset sujuvista palveluista.
Delfoi Planner Sote on sosiaali- ja terveydenhuollon palvelutuotannon suunnittelu ja -ohjausratkaisu.